Crafting Security: The Intricate Production Process of Bulletproof Glass
Material Selection: The production process begins with meticulous selection of high-quality materials, including layers of laminated glass and polycarbonate.
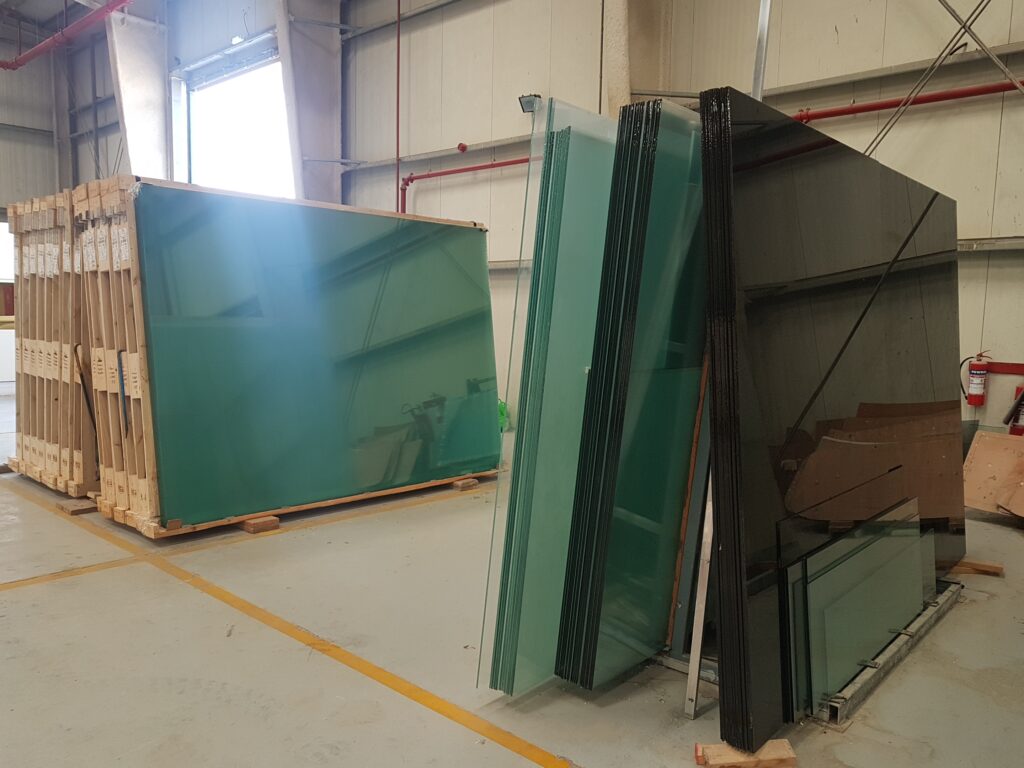
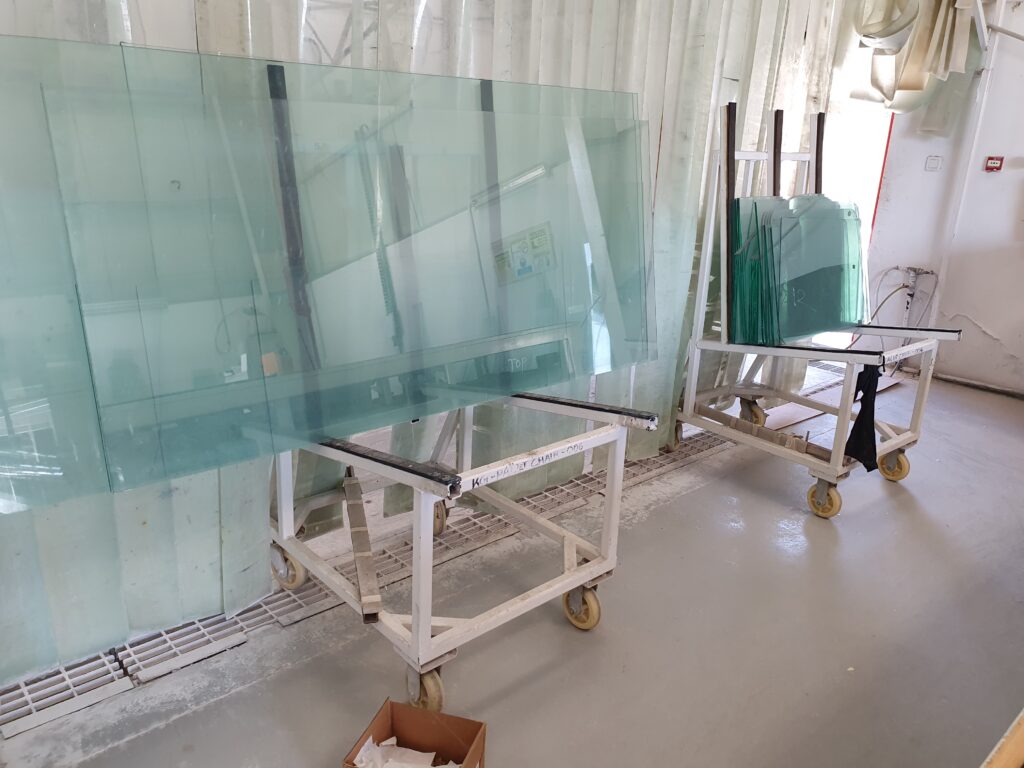
Cutting and Shaping: The composite material is precisely cut and shaped according to specific design requirements, ensuring accuracy and consistency in the final product.
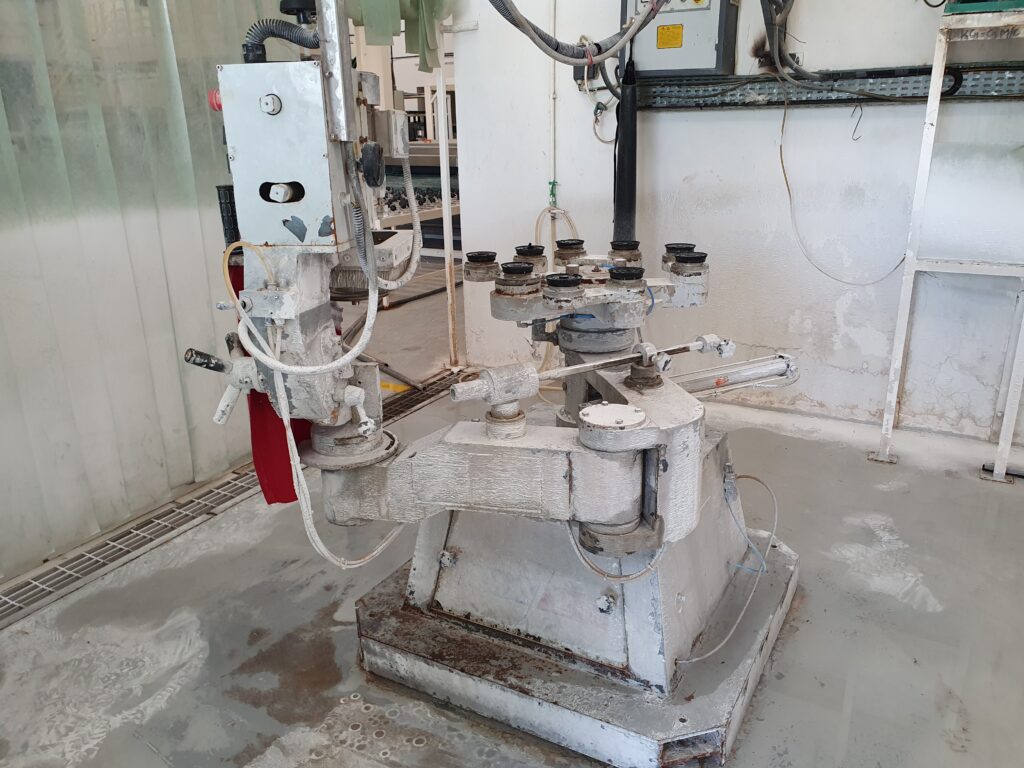
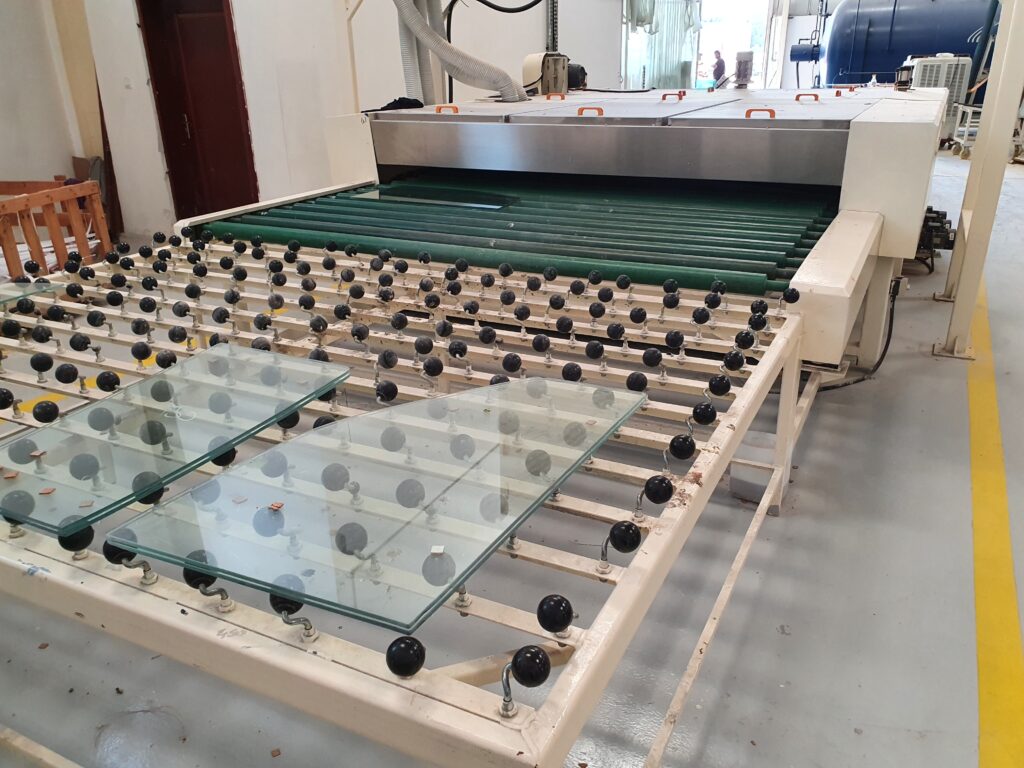
Layering and Bonding: Multiple layers of glass and polycarbonate sheets are precisely arranged and bonded together using specialized adhesives to form a robust composite.
Lamination: The layered structure undergoes lamination, a crucial step where the materials are subjected to high pressure and heat to create a cohesive and resilient unit.
Pressing and Heating: The assembly undergoes a controlled pressing and heating process, promoting the fusion of layers and enhancing the overall strength of the bulletproof glass.
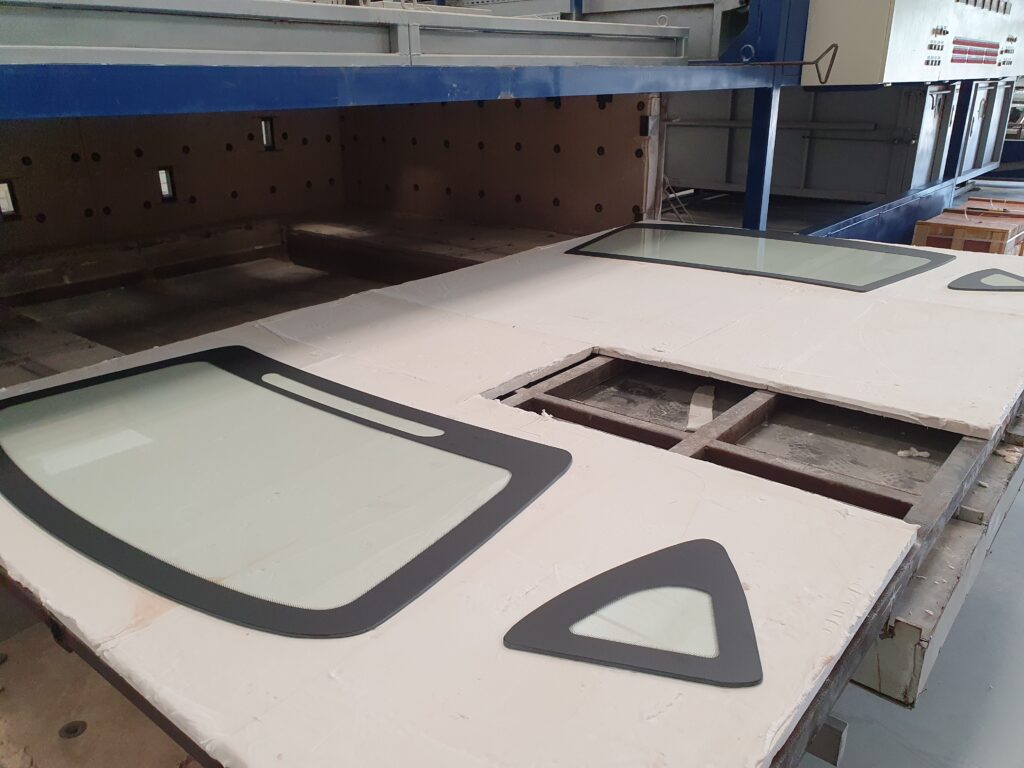
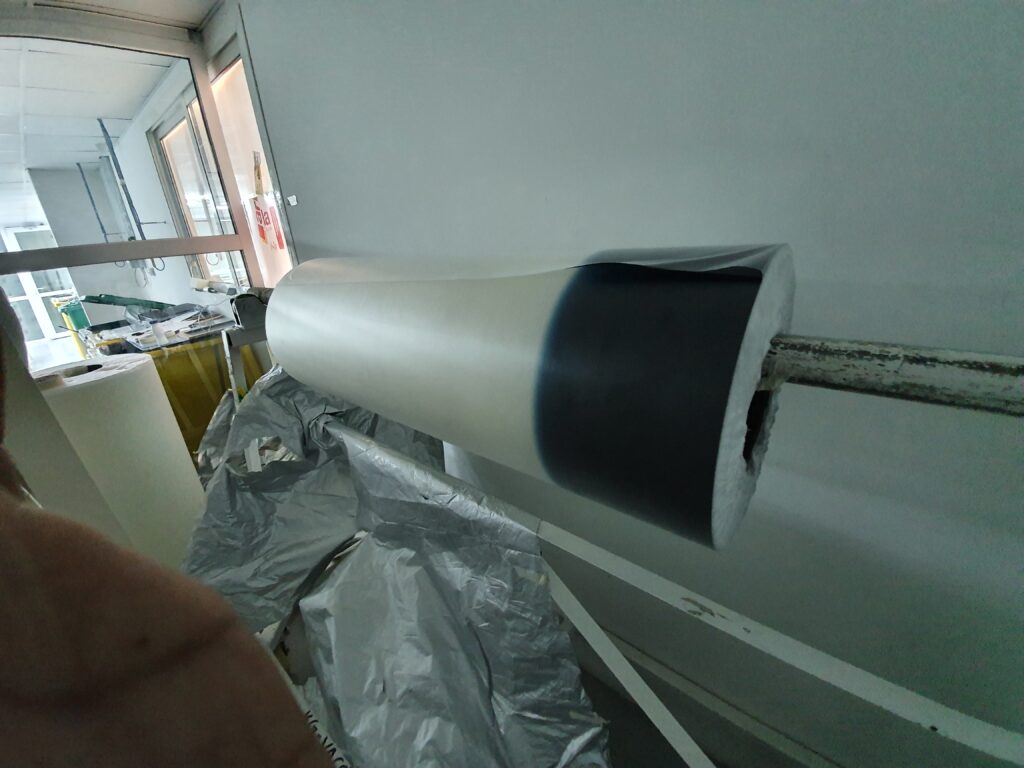
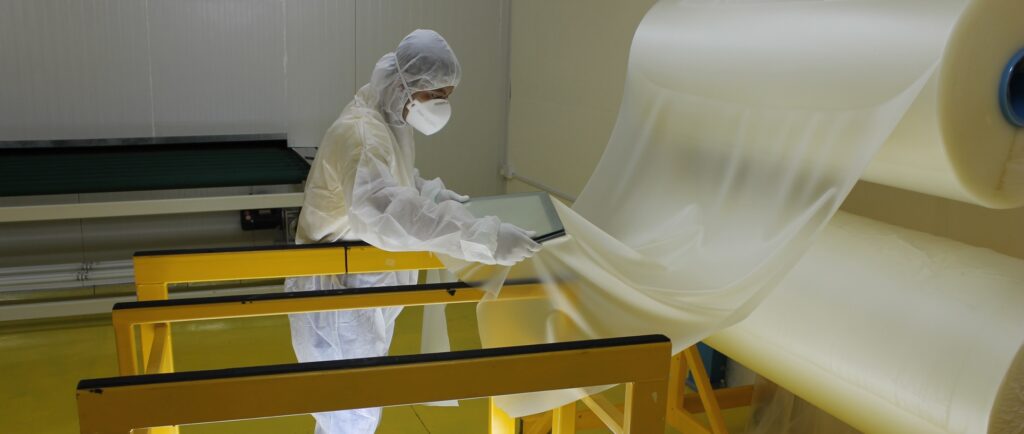
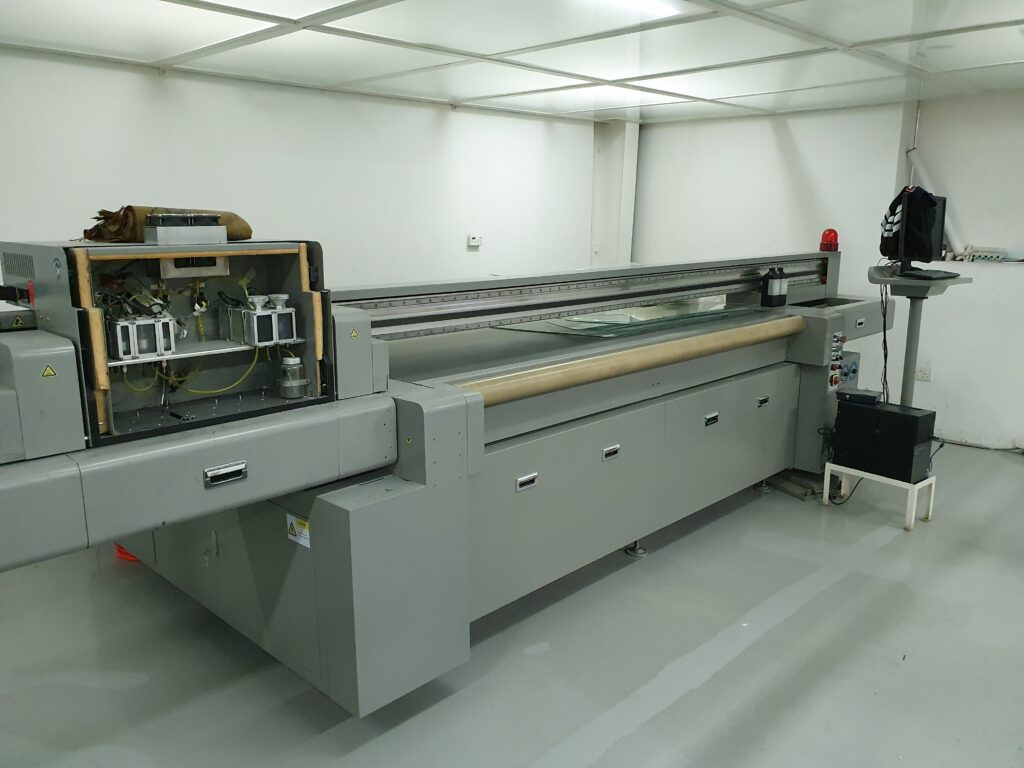
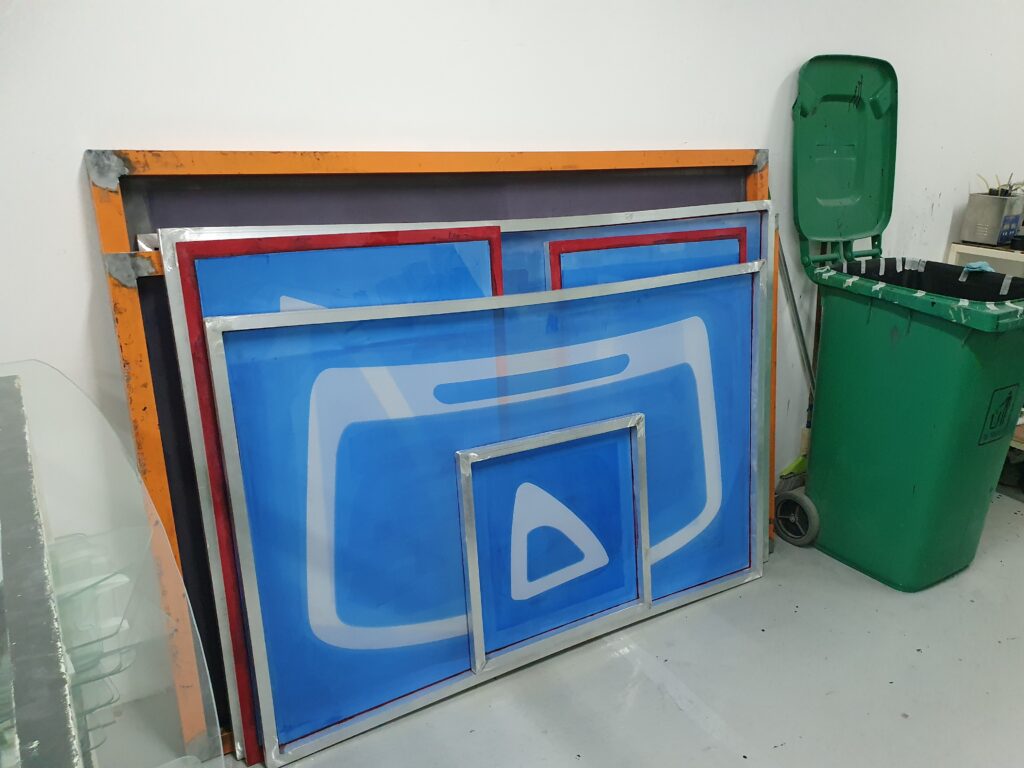
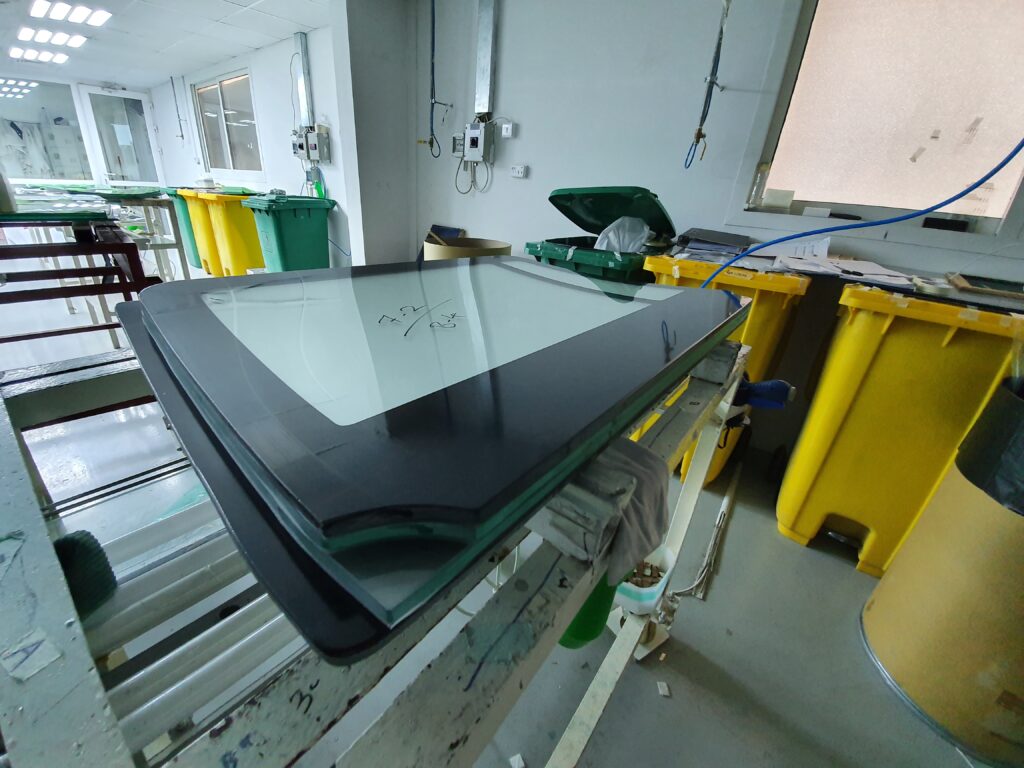

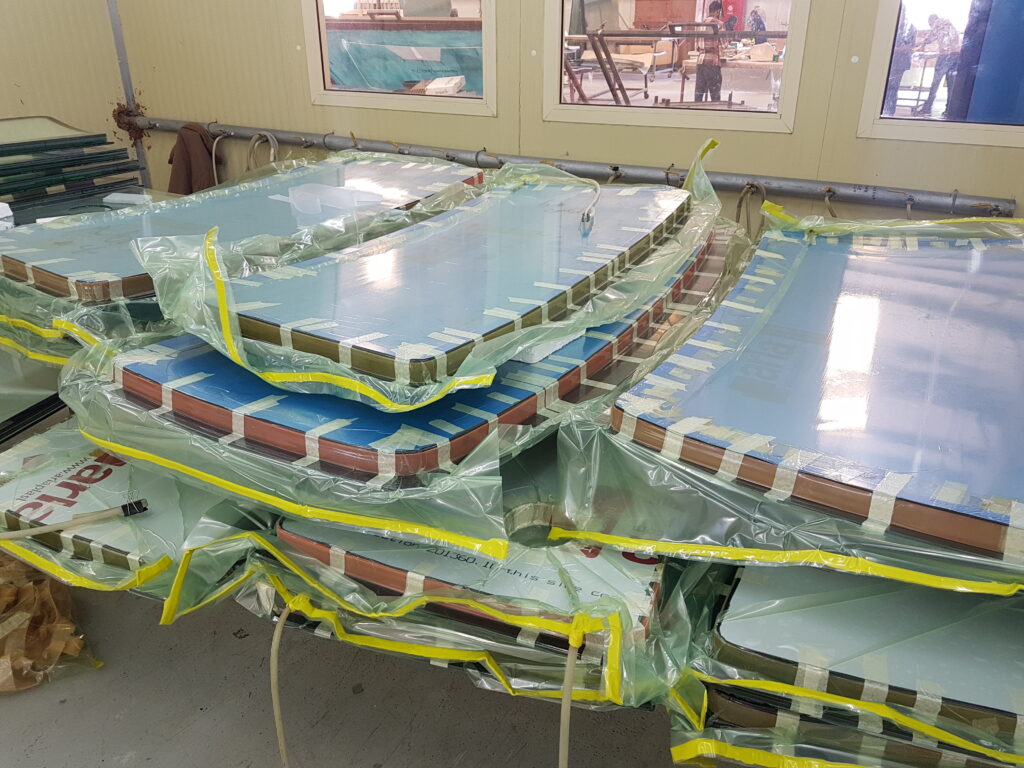
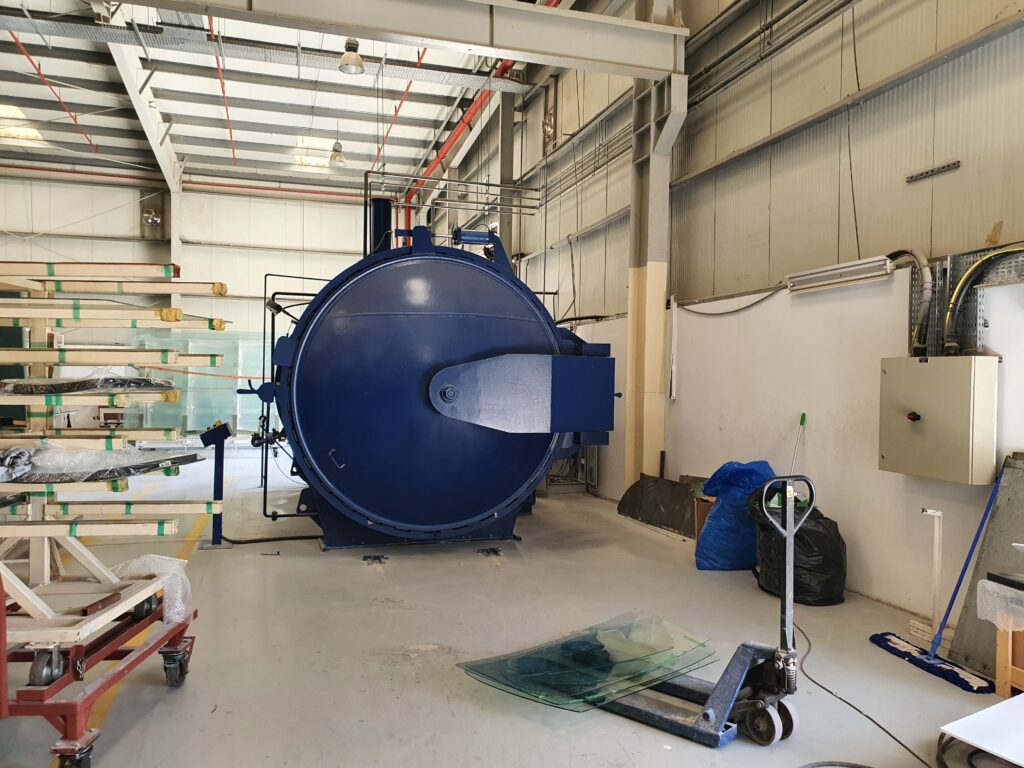
Quality Control Testing: Rigorous testing, including ballistic impact, ensures the bulletproof glass meets or exceeds specified safety standards and performance criteria.
Final Inspection: Each finished bulletproof glass unit undergoes a meticulous final inspection to verify quality, clarity, and adherence to customer specifications.
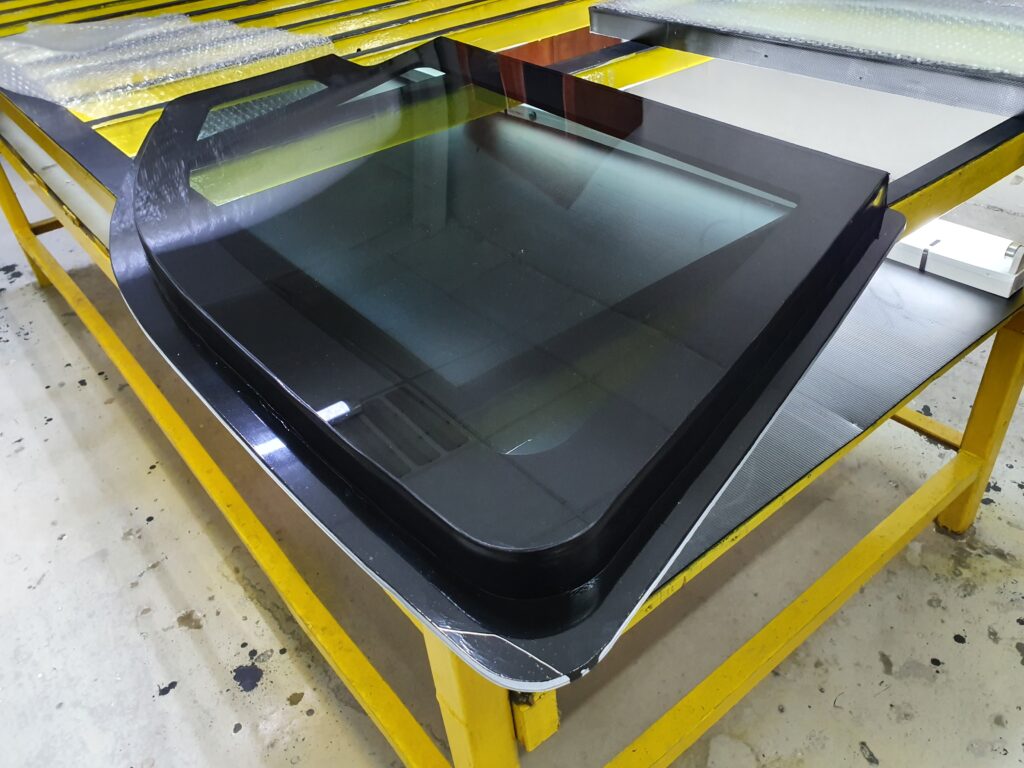


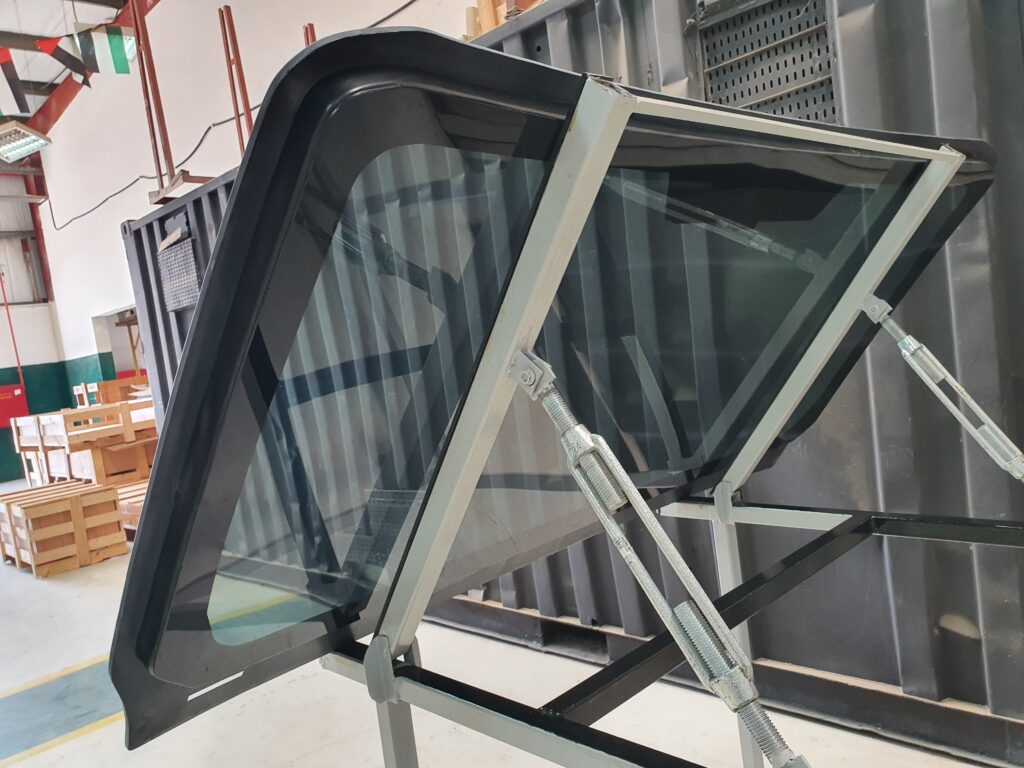
Packaging and Shipping: The completed bulletproof glass units are carefully packaged to prevent damage during transit and shipped to clients worldwide, ready to provide top-tier security.
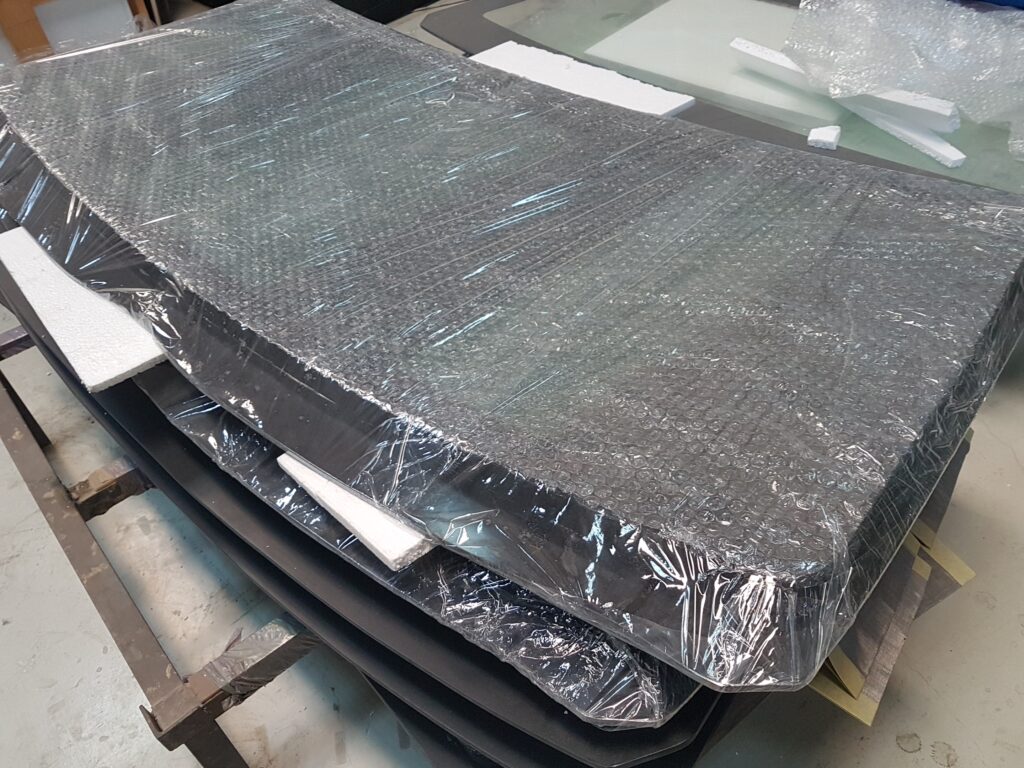
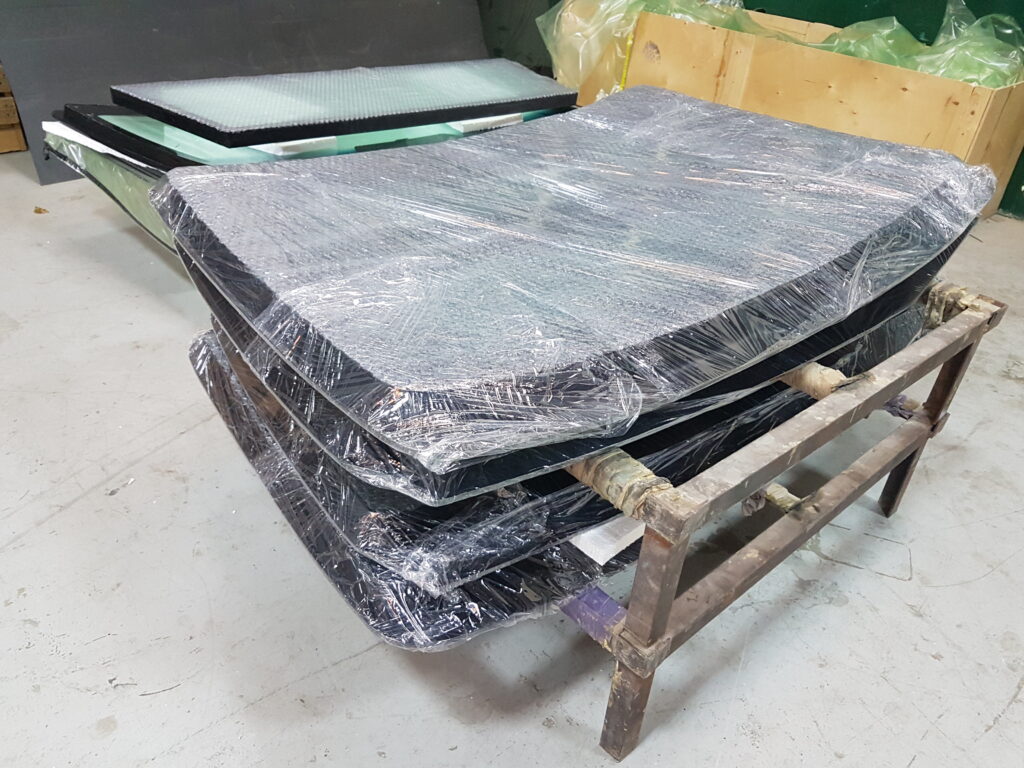

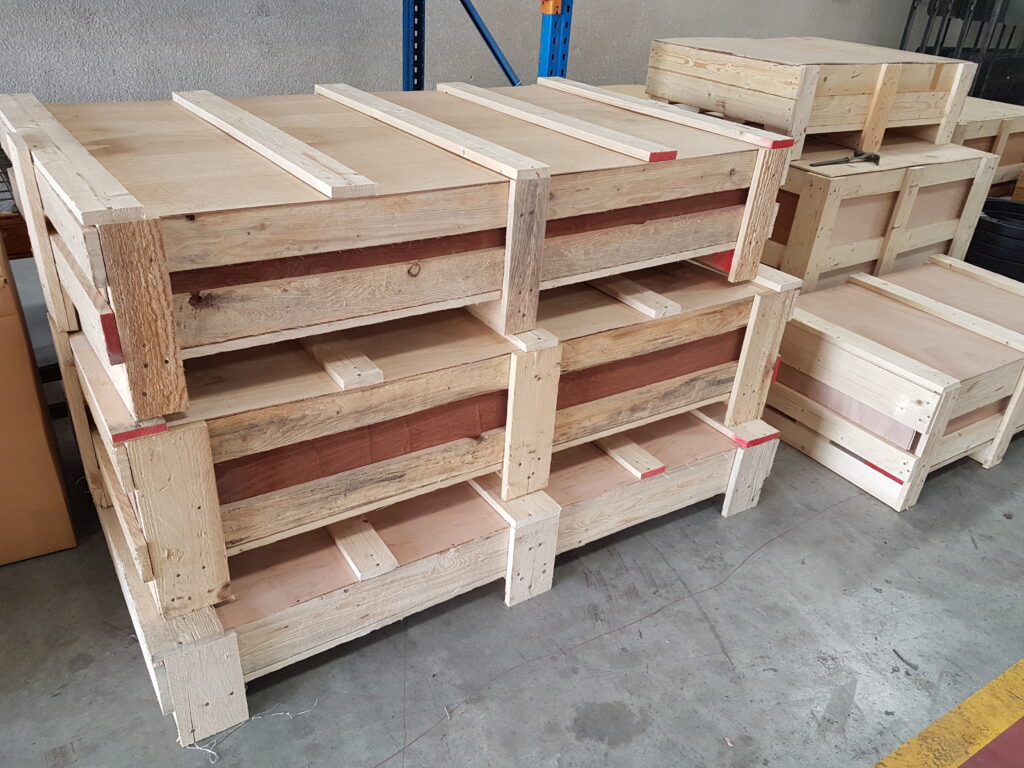

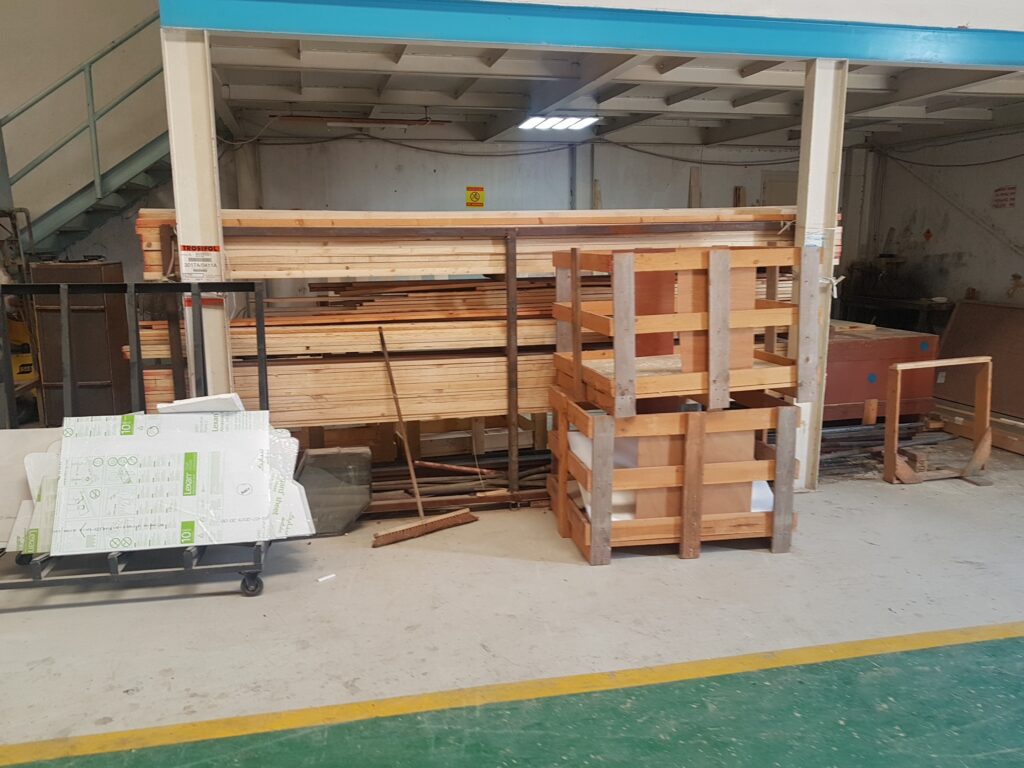
The manufacturing process of bulletproof glass is an intricate and highly skilled job that demands precision at every stage. From the meticulous selection of materials to the complex lamination process, each step requires specialized knowledge and expertise. Skilled technicians carefully layer and bond materials, subjecting them to controlled pressing and heating to achieve optimal cohesion. The artistry comes into play during the cutting and shaping stages, where the composite material is crafted to exact specifications with an acute attention to detail.
Moreover, the sophistication of the manufacturing process extends to the critical quality control measures in place. Rigorous testing, including ballistic impact assessments, ensures that the bulletproof glass meets stringent safety standards. The application of specialized coatings and the final inspection demand a keen eye for perfection. Ultimately, crafting bulletproof glass is not just a manufacturing process; it’s a highly skilled endeavor that combines technical expertise with a commitment to delivering security solutions of the highest caliber.
Innovating Security: Advancements Through Research and Development
In the dynamic landscape of armored vehicles, Dynamic Defense Solutions spearheads research and development efforts to continually refine and innovate bulletproof glass tailored for new armored cars. Our dedicated team engages in comprehensive research to identify the latest materials, technologies, and manufacturing processes that can elevate the protective capabilities of bulletproof glass. By staying ahead of emerging trends and potential threats, we ensure that our solutions are not only robust and reliable but also adaptable to the evolving needs of modern armored car designs.
The research and development initiatives extend beyond mere protection, encompassing considerations for weight reduction, optical clarity, and overall vehicle performance. Through rigorous testing and analysis, we fine-tune our formulations, explore innovative composites, and integrate the latest advancements in glass technology. This commitment ensures that our bulletproof glass for new armored cars strikes the optimal balance between cutting-edge security features and seamless integration, contributing to the overall safety and sophistication of the next generation of armored vehicles.
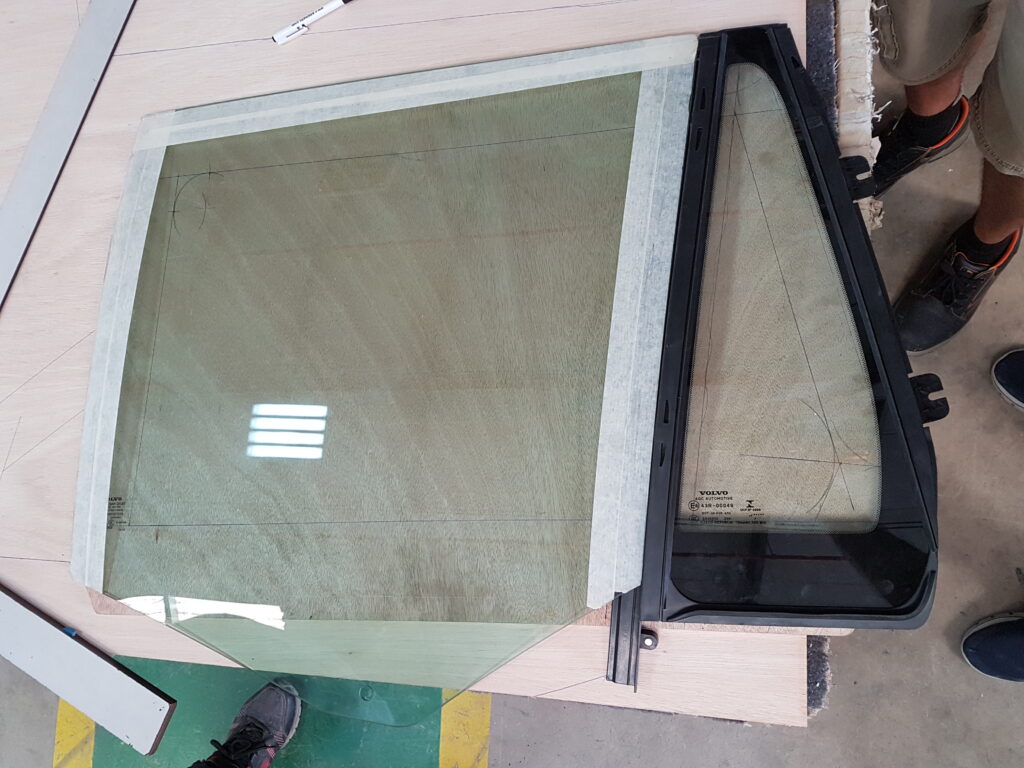
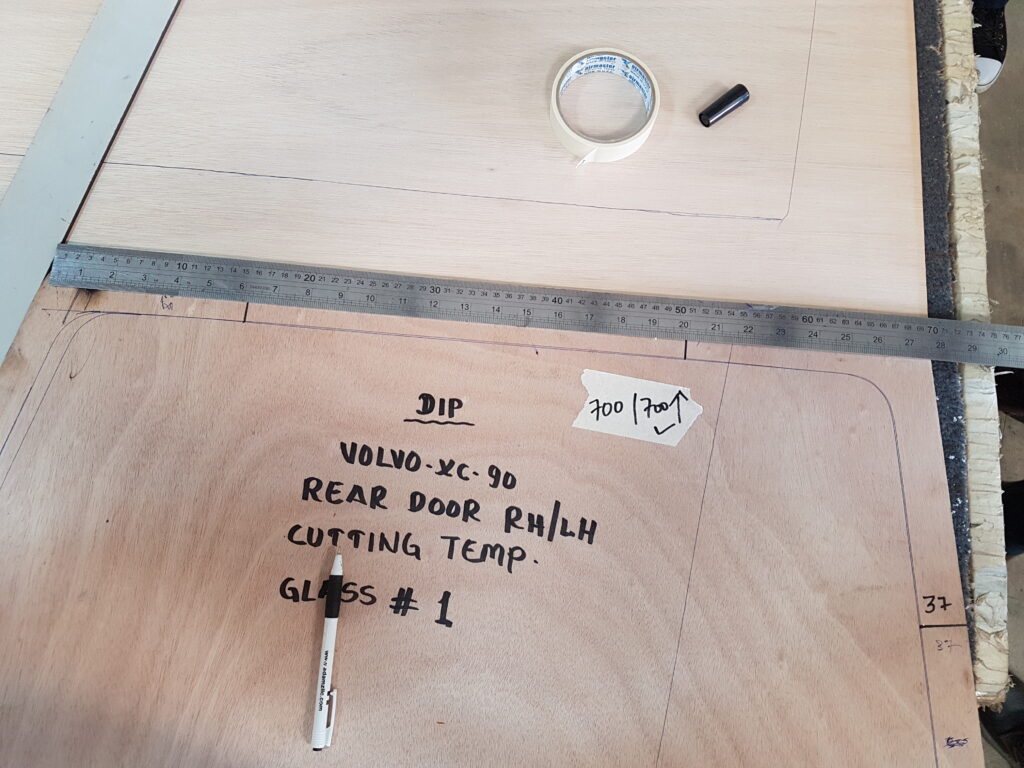
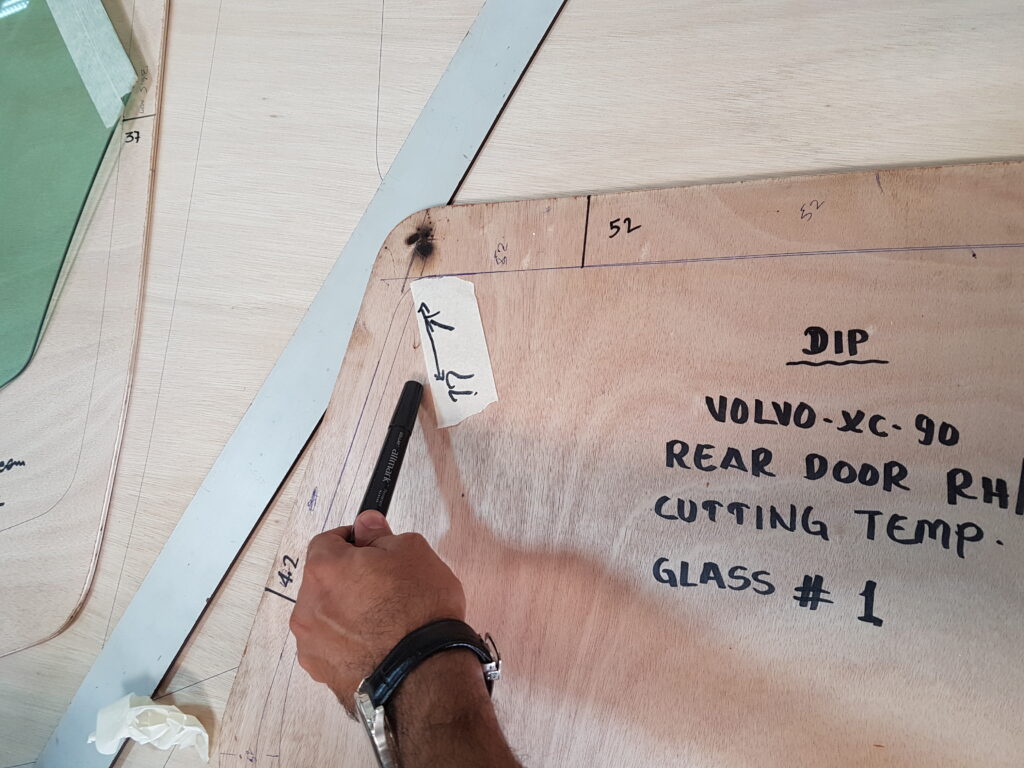
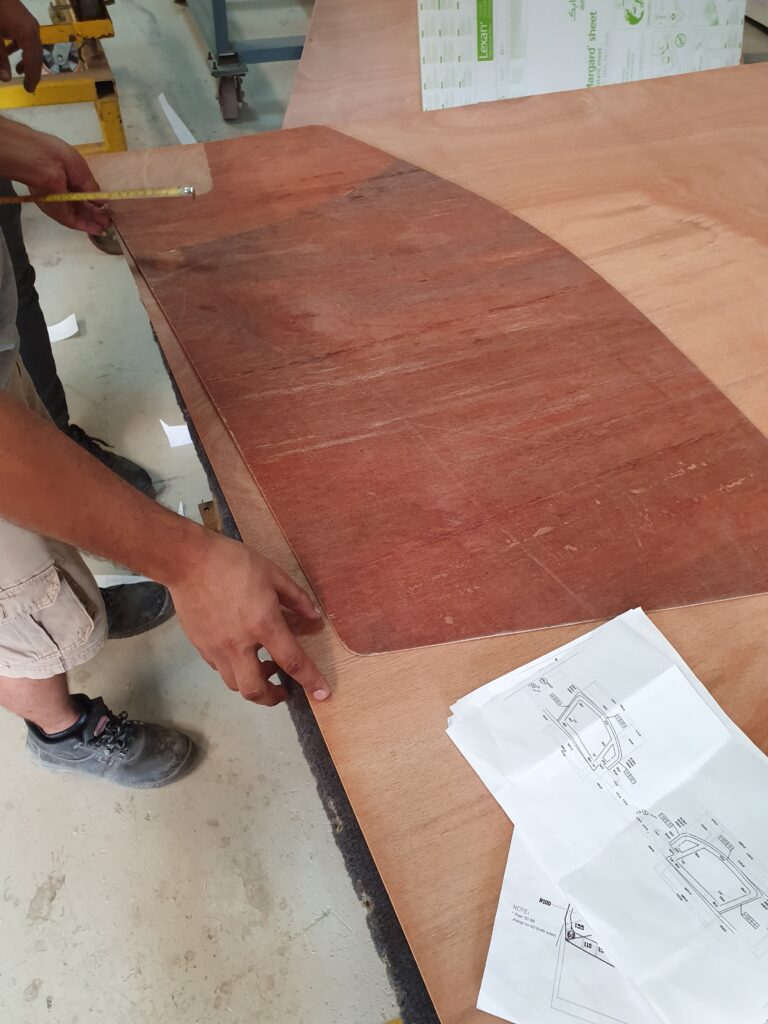
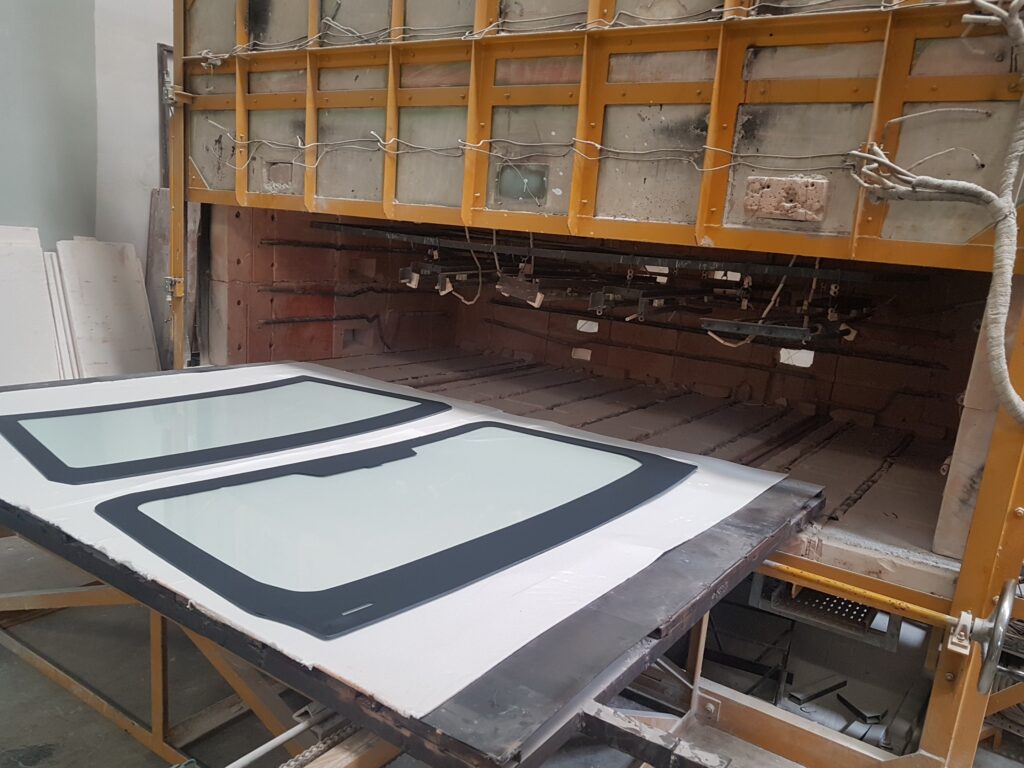
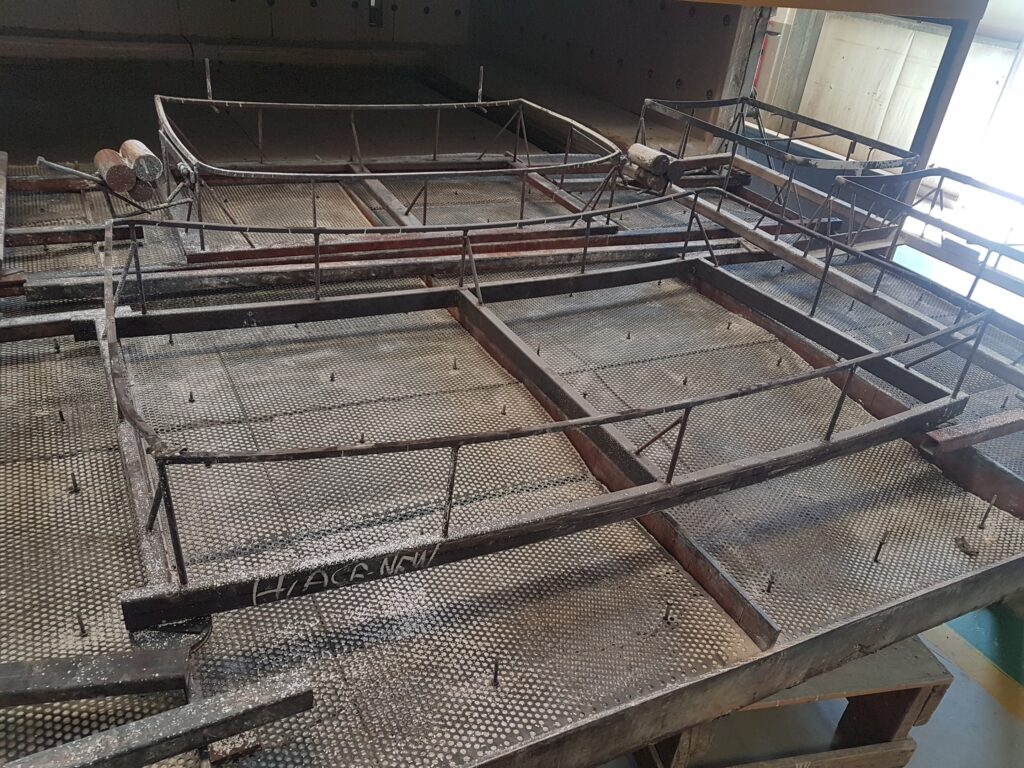
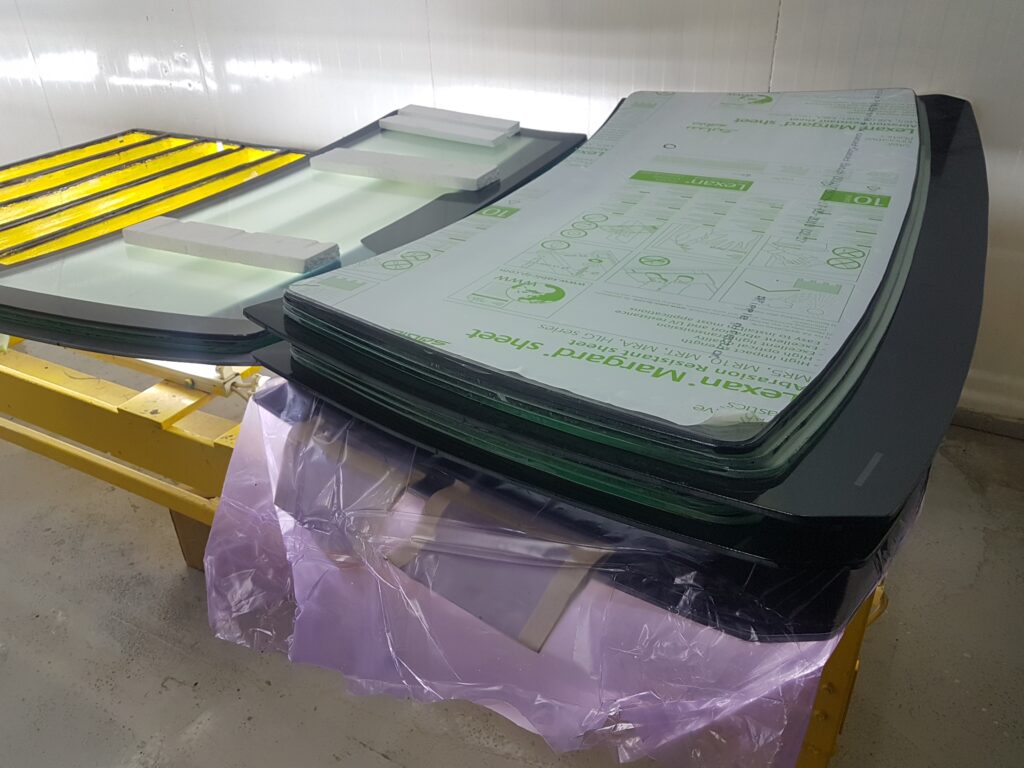